High-Quality Blow Molding Machine Manufacturer for Diverse Industrial Needs
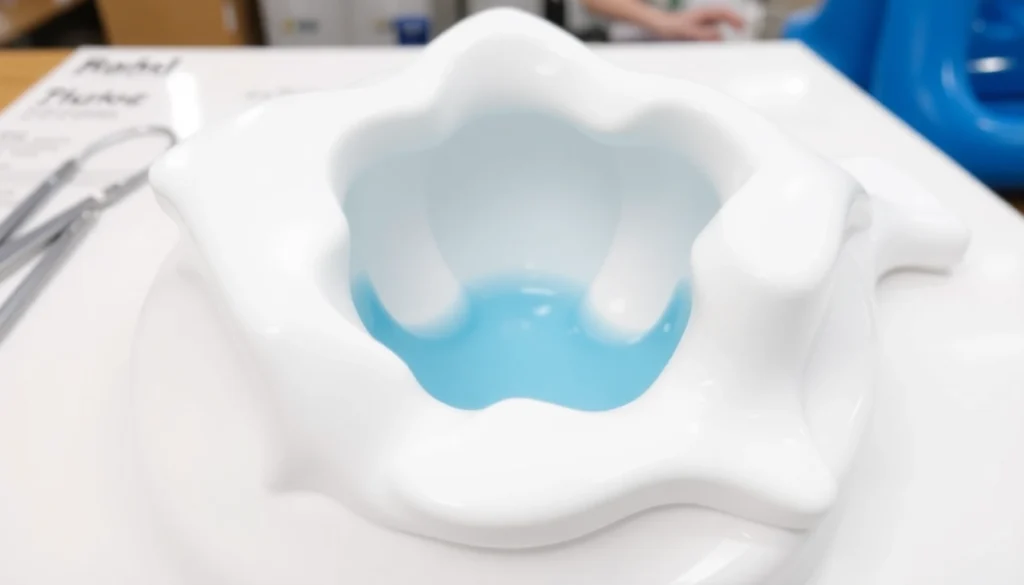
Understanding Blow Molding Technology
Basics of Blow Molding Process
The blow molding process is a widely utilized manufacturing technique for producing hollow plastic items such as bottles, containers, and various other applications. It typically involves three main stages: extrusion, molding, and cooling. In the extrusion phase, plastic material is melted and formed into a parison, which is a hollow tube of thermoplastic. Once the parison is formed, it is placed into a mold, and air is introduced to inflate the parison into the shape of the mold cavity. Finally, the molded piece is cooled and then ejected from the mold, resulting in a finished product.
There are several types of blow molding methods, including extrusion blow molding (EBM), injection blow molding (IBM), and stretch blow molding (SBM). Each method has its particular advantages, depending on the desired characteristics of the final product, production volume, and the material used.
Types of Blow Molding Machines
When it comes to blow molding machines, manufacturers can choose from various options based on their specific needs. Here are some common types:
- Extrusion Blow Molding Machines: Used for producing large and complex shapes, these machines are highly efficient and capable of handling various plastic materials. They are particularly suitable for bottles and containers of various sizes.
- Injection Blow Molding Machines: Ideal for making small to medium-sized products, IBM machines use a combination of injection molding processes and blow molding techniques to create hollow plastic items. This method is often used for high-precision medical and cosmetic products.
- Stretch Blow Molding Machines: Used primarily for producing PET bottles, stretch blow molding enhances product strength and clarity. This method involves stretching the parison and blowing it into the mold, resulting in thinner walls and enhanced durability.
Applications in Various Industries
Blow molding technology is pivotal across numerous industries, including:
- Food and Beverage: The production of bottles and containers for soft drinks, water, and food products.
- Pharmaceutical: Creating precise, reliable containers for medicines and health-related products.
- Cosmetics: Manufacturing aesthetically appealing containers for personal care products.
- Toys: Producing lightweight and durable plastic toys for children.
- Automotive: Making components such as fuel tanks and interior panels.
Choosing the Right Blow Molding Machine Manufacturer
Key Factors to Consider
When selecting a blow molding machine manufacturer, there are several critical aspects to evaluate to ensure quality and suitability for your production needs:
- Experience and Expertise: Choose a manufacturer with years of experience and a diverse portfolio showcasing their capability across various industries.
- Technology and Innovation: Assess the technological advancements incorporated in their machines, such as energy efficiency, automation features, and integration of smart technologies.
- Customer Support: Verify the level of customer support provided, including after-sales service, training, and availability of spare parts. Reliable support can significantly impact the longevity and productivity of your equipment.
- Customization Options: Find manufacturers willing to tailor their machines to meet specific production requirements and product specifications.
- Pricing and ROI: Evaluate the cost of the machines against their long-term benefits and ROI. Sometimes, spending a bit more upfront can lead to substantial savings over time.
Comparing Industry Leaders
Several key players dominate the blow molding machine manufacturing industry. Companies like Uniloy, Wilmington Machinery, Jomar Corporation, and Bekum Maschinenfabrik GmbH are known for their cutting-edge technology and extensive range of machines.
For instance, Blow Molding Machine Manufacturer, Uniloy stands out as a global leader in blow molding technologies, offering four unique blow molding technologies along with blow molds and associated tooling. Wilmington Machinery specializes in high-speed rotary extrusion blow molding systems, emphasizing speed and efficiency. Each manufacturer has its strengths, and understanding these distinctions can help businesses select the right partner for their needs.
Customer Testimonials and Success Stories
Gathering testimonials and case studies from existing customers can provide invaluable insights into a manufacturer’s reliability and service. Engaging with current users about their experiences, the efficiency of the equipment, and the support received can guide prospective buyers. For instance, many customers of Jomar Corporation praise its high-quality injection blow molding machines, highlighting their ability to produce durable medical parts with exceptional precision.
Innovations in Blow Molding Machinery
Smart Technology Integration
The incorporation of smart technology in blow molding machinery is on the rise, offering manufacturers improved operational efficiencies. Automation features, including real-time monitoring systems and predictive maintenance alerts, are designed to optimize production workflows and reduce downtime. Smart factories integrate these machines with IoT devices, enabling better management of supply chains and inventory levels.
For example, innovative software solutions can help operators monitor processes and adjust settings dynamically to ensure optimal machine performance. This level of real-time data collection not only enhances efficiency but also leads to higher product quality through better process control and management.
Environmental Sustainability in Manufacturing
With sustainability becoming increasingly vital in manufacturing, many blow molding machine manufacturers are focusing on eco-friendly practices. This includes the development of machines that utilize recyclable materials and processes that minimize waste production.
For instance, companies are now offering equipment capable of working with bio-based plastics or recycled materials that further reduce carbon footprints. By adopting such practices, manufacturers not only adhere to regulatory requirements but also appeal to a more environmentally conscious consumer base.
Future Trends in Blow Molding Technology
The blow molding industry is expected to evolve rapidly, influenced by technological advancements and changing consumer preferences. Here are some anticipated trends:
- Increased Use of Automation: Automation will continue to dominate, with an increasing number of facilities utilizing robotics and AI for tasks such as quality control and packing.
- Simplification of Production Processes: Manufacturers will strive for streamlined processes that enhance productivity, efficiency, and reduce costs. This could include more user-friendly interfaces on machines.
- Integration of Advanced Materials: The industry will likely see continued experimentation with advanced materials that offer improved performance characteristics and sustainability benefits.
Maintenance and Upkeep of Blow Molding Machines
Essential Maintenance Practices
Routine maintenance is crucial to ensure blow molding machines operate efficiently and have a long lifespan. Here are some essential practices:
- Regular Inspections: Scheduled inspections help identify potential issues before they escalate into major repair requirements.
- Cleaning: Keeping the machinery clean prevents the buildup of resin and other contaminants that might affect production quality.
- Lubrication: Regular lubrication of moving parts minimizes wear and prolongs the lifespan of machine components.
- Calibration: Periodic calibration ensures that the machinery operates within specified parameters, contributing to consistent product quality.
Common Issues and Solutions
Even the best-maintained machines can experience issues. Here are some common problems and potential solutions:
- Mold Leakage: If leaks occur, checking seals and fittings should be the first step. Replacing worn gaskets often solves this problem.
- Inconsistent Product Quality: Variability can arise from improper temperature settings or fluctuating material quality. Regular calibration and material analysis may be needed.
- Machine Jams: This can often be traced back to debris in the machinery or improper loading of materials. Cleaning and training operators can help minimize jams.
When to Seek Professional Help
While many maintenance tasks can be handled in-house, certain complex issues may necessitate professional intervention. Signs that professional assistance is needed include:
- Repeated breakdowns despite regular maintenance.
- Inability to troubleshoot or diagnose issues.
- Significant changes in machine performance.
Maximizing Efficiency with Blow Molding Solutions
Optimizing Production Workflow
Efficiency can be significantly enhanced through workflow optimization. This may include streamlining the layout of the production line, ensuring that machines are suitably spaced for logistical ease, and implementing just-in-time manufacturing practices to minimize surplus inventory costs.
Employing comprehensive scheduling software can also help manufacturers make the most of their available resources, thus maximizing production output while reducing idle time.
Cost-Effectiveness and ROI
Blow molding can offer significant cost advantages when executed correctly. Investing in high-quality machinery that is energy-efficient, along with strategic production planning, can reduce operating costs. Additionally, understanding the ROI through precise calculations based on throughput, labor costs, and machine performance can help businesses make informed decisions regarding investments in new technology or machinery upgrades.
Case Studies of Effective Implementation
When considering a blow molding machine, it’s useful to reference case studies that illustrate successful implementation. For example, a large beverage manufacturer recently adopted a fully automated blow molding line that resulted in a 25% reduction in cycle times and a 15% decrease in material waste, demonstrating clear financial benefits. Such examples underline the potential gains from investing in cutting-edge blow molding solutions.