Choosing the Right Commercial Metal Roofing: Advantages, Styles, and Applications
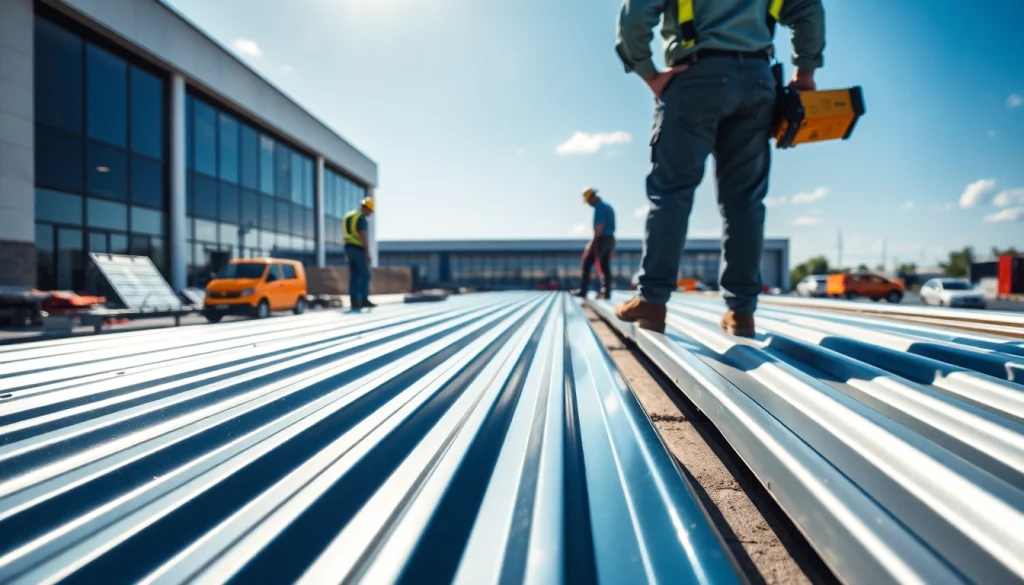
1. Understanding Commercial Metal Roofing
In the ever-evolving landscape of commercial construction, commercial metal roofing has emerged as a popular choice for business owners and builders alike. It combines durability, aesthetic appeal, and a host of functional benefits that can greatly enhance a commercial facility’s effectiveness. This article delves deep into the multifaceted world of commercial metal roofing, offering insights into its definition, materials used, common myths, and the diverse benefits it offers for commercial constructions.
1.1 Definition and Benefits of Commercial Metal Roofing
Commercial metal roofing refers to roofing systems made from metal materials, typically steel or aluminum, designed specifically for commercial buildings, including warehouses, industrial plants, and retail outlets. Its unique properties make it an excellent choice for large structures that demand durability and energy efficiency.
Among the myriad of benefits associated with commercial metal roofing, here are some noteworthy aspects:
- Durability: Metal roofs are remarkably resistant to harsh weather conditions, including extreme heat, heavy winds, and moisture. This resilience translates into a longer lifespan—often exceeding 50 years—compared to traditional roofing materials.
- Energy Efficiency: Metal roofs reflect solar heat, which can contribute to lower energy costs. Many commercial metal roofing systems are designed to integrate insulation, further enhancing thermal performance.
- Low Maintenance: Unlike wooden or shingled roofs that require frequent repairs, metal roofs generally require minimal maintenance, which can save businesses both time and money in the long run.
- Environmentally Friendly: Many metal roofing products are made from recycled materials and are recyclable at the end of their life cycle, making them a sustainable choice for environmentally-conscious businesses.
1.2 Key Materials Used in Commercial Metal Roofing
Various materials can be used in the construction of commercial metal roofing systems, each with unique properties. Here are some of the most commonly used materials:
- Steel: Often galvanized or coated for additional rust resistance, steel is one of the most widely used materials in commercial metal roofing due to its strength and affordability.
- Aluminum: Lightweight and resistant to corrosion, aluminum is ideal for coastal areas where salt water can lead to rapid deterioration of other materials.
- Copper: While more expensive, copper roofing develops a protective patina over time, making it highly durable and visually appealing.
- Zinc: Known for its longevity, zinc is another metal utilized for roofing due to its non-corrosive properties and ability to self-heal when scratched.
1.3 Common Myths about Metal Roofing Debunked
Despite its numerous benefits, misconceptions about metal roofing persist. Here, we debunk some common myths:
- Myth 1: Metal roofs are noisy during rain and hail.
Fact: Proper insulation reduces sound transmission, making them comparably quiet to traditional roofing materials. - Myth 2: Metal roofs attract lightning.
Fact: Metal does not attract lightning; in fact, they can be safer than traditional roofs as they can dissipate electricity without causing fire. - Myth 3: Metal roofing is too expensive.
Fact: While the upfront costs may be higher, the longevity and low maintenance expenses result in cost savings over time.
2. Types of Commercial Metal Roofing Systems
With a range of options available, businesses can choose from various commercial metal roofing systems that align with their specific needs, aesthetic preferences, and budgets. This section will explore some popular types of commercial metal roofing systems.
2.1 Exposed Fastener vs. Hidden Fastener Systems
Metal roofing systems can be categorized based on the fastening methods used—exposed or hidden. Both types have their benefits and limitations:
- Exposed Fastener Systems: These roofs utilize screws that are visible on the surface of the panels. They are typically easier to install and less costly, making them an attractive option for budget-conscious commercial projects.
- Hidden Fastener Systems: Screw fastening is concealed within the panels, leading to a cleaner aesthetic appeal. This method might be slightly more expensive but offers superior waterproofing and less risk of leaks due to hidden fastener integrity.
2.2 Insulated Panels and Their Advantages
Insulated metal panels (IMPs) comprise a layer of insulation sandwiched between two metal panels. Their design offers several distinct advantages:
- Thermal Efficiency: IMPs provide excellent insulation, reducing heating and cooling costs significantly.
- Quick Installation: These panels arrive ready to install, reducing construction time and labor costs.
- Versatile Applications: With an appealing finish, IMPs are suitable for various commercial buildings, ranging from warehouses to retail spaces.
2.3 Customization Options: Colors and Finishes
One of the significant advantages of choosing commercial metal roofing is the plethora of customization options. Business owners can select from various colors and finishes to ensure that the roofing complements their building’s design:
- Color Options: Metal roofs are available in a wide array of colors, offering flexibility in matching existing buildings or creating brand identity through color schemes.
- Finishing Techniques: Specialized coatings can enhance the roof’s durability, ranging from painted finishes that provide aesthetic appeal to metallic finishes that reflect sunlight and reduce heat.
3. Installation Process of Commercial Metal Roofing
A well-executed installation process is crucial for the success and longevity of a commercial metal roofing system. This section outlines the key steps involved in the installation of these roofing systems.
3.1 Pre-installation Considerations and Planning
Prior to installation, several factors must be assessed to ensure a smooth process:
- Building Assessment: Evaluating the existing structure, including the roofing system and its condition, is critical. This step helps determine any necessary repairs before new installation.
- Material Selection: Selecting the right type and gauge of metal, based on the building’s size, climate, and budget, is essential for functionality and aesthetics.
- Permits and Local Codes: Understanding local building codes and obtaining necessary permits can prevent legal issues and ensure compliance.
3.2 Step-by-Step Installation Guide
The installation of commercial metal roofing typically follows a systematic approach:
- Clear the Roof: All debris such as old roofing materials and blockages that can hinder installation should be removed.
- Install Underlayment: A water-resistant underlayment is placed to provide an additional layer of protection against leaks.
- Install Metal Panels: Begin laying down the metal panels, starting from the eave and progressing upwards. Ensure that each panel overlaps the preceding one to facilitate proper drainage.
- Fastening: Use the selected fastening system to secure each panel, taking care to follow the manufacturer’s guidelines for spacing and handling.
- Edge and Ridge Caps: Install edge and ridge caps to finalize the roof and ensure a watertight seal.
3.3 Safety Measures During Installation
Safety is essential during any roofing installation. The following measures should always be taken:
- Personal Protective Equipment (PPE): Workers should wear appropriate gear, including helmets, harnesses, and slip-resistant footwear.
- Weather Considerations: Installation should not be performed during inclement weather, such as strong winds or rain, to prevent accidents.
- Training: Ensure that all personnel involved in the installation are trained and knowledgeable about the equipment and safety protocols.
4. Maintenance and Longevity of Metal Roofs
Maintaining a commercial metal roof is crucial to maximizing its lifespan and performance. This section will detail essential maintenance practices, signs of wear, and the expected lifespan of various materials.
4.1 Routine Maintenance Tips for Commercial Metal Roofing
Regular maintenance can extend the life of commercial metal roofing significantly. Here are some maintenance tips:
- Regular Inspections: Conduct inspections at least twice a year and after severe weather events to identify issues early.
- Cleaning: Remove debris, leaves, and dirt from the surface and gutters to allow for proper water drainage and prevent rust.
- Check Fasteners: Inspect the fastening systems periodically to ensure they are secure and not showing signs of corrosion or damage.
4.2 Signs of Wear and When to Replace
Recognizing the signs of wear can help prevent more significant damage down the line. Here are some indicators that it may be time to consider replacement:
- Visible Rust or Corrosion: Surface rust and corrosion are warnings that the roof’s integrity may be compromised.
- Loose or Missing Panels: Panels that are no longer securely fastened can lead to leaks and further damage.
- Higher Energy Bills: A sudden increase in energy costs may indicate that insulation is failing or that water intrusion is affecting the structure.
4.3 The Lifespan of Different Metal Roofing Materials
The lifespan of a commercial metal roof varies based on material choice:
- Steel: Typically lasts 40-60 years when properly installed and maintained.
- Aluminum: Can last 50 years or longer, especially suitable for coastal environments.
- Copper: A lifespan of over 100 years is common, making it one of the longest-lasting options.
- Zinc: Known for its longevity, zinc roofs can also last upwards of 80 years.
5. Cost Considerations and ROI of Metal Roofing
Understanding the financial aspects of commercial metal roofing is vital for any business. This section will examine what influences costs, how metal roofing compares to other materials, and the potential return on investment.
5.1 Factors Influencing the Cost of Commercial Metal Roofing
Several factors can influence the overall cost of installing a metal roofing system:
- Material Choice: Different metals come at different price points. For instance, aluminum is generally more expensive than steel but offers distinct benefits.
- Roof Size: The larger the roof area, the more materials and labor are required, impacting costs.
- Complexity of Design: Roofs with multiple angles, slopes, or custom features can increase installation complexity and cost.
- Location: Construction costs can vary based on regional labor rates and availability of materials.
5.2 Comparing Metal Roofing Costs with Other Roofing Types
When comparing metal roofing to alternative materials, certain distinctions must be noted:
- Asphalt Shingles: Usually less expensive initially, but their lifespan is significantly shorter—15-30 years—resulting in higher long-term costs.
- Tile Roofing: While aesthetically pleasing, tile can be more costly to install and repair, with similar lifespans as metal roofing.
- Built-Up Roofing (BUR): Generally lower upfront costs but may require more extensive maintenance and upkeep compared to metal roofs.
5.3 Assessing Long-term Savings and Energy Efficiency
Investing in commercial metal roofing can lead to substantial long-term savings. Key factors include:
- Energy Efficiency: Lower monthly energy costs due to superior insulation and heat reflection.
- Insurance Savings: Some insurance companies offer lower premiums for businesses using durable metal roofing systems, which can lead to substantial savings.
- Reduced Maintenance Costs: Given their longevity and low maintenance requirements, metal roofs can substantially reduce repair and replacement costs over time.
In conclusion, commercial metal roofing presents compelling advantages for business owners looking to optimize their building’s performance while maintaining aesthetic appeal. With a variety of materials, configurations, and customization options available, metal roofs are an excellent investment backed by a combination of durability, energy efficiency, and reduced maintenance.