High-Quality Precision Die Cutting Services for Custom Solutions
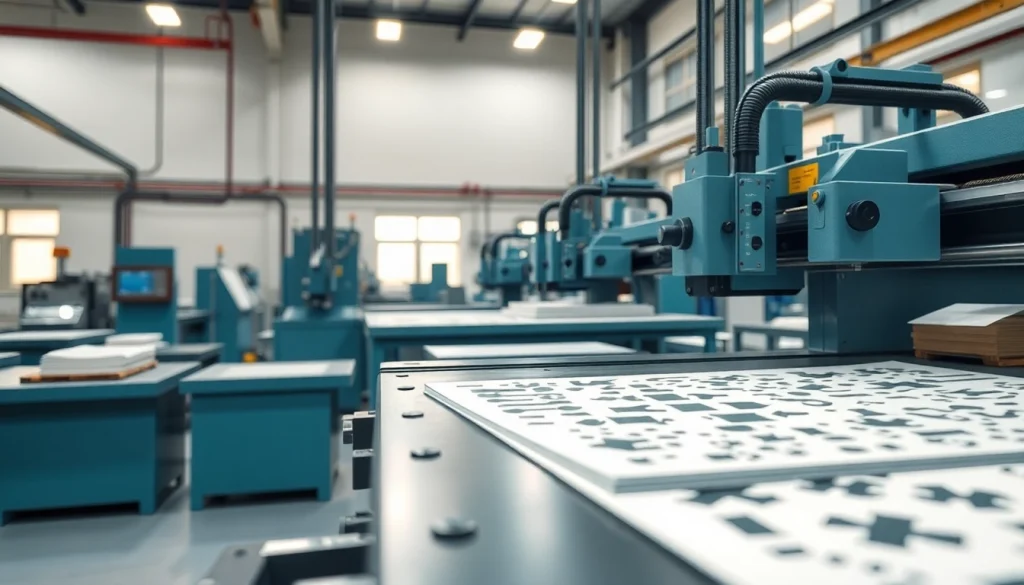
Understanding Precision Die Cutting
Precision die cutting is a pivotal manufacturing process that specializes in cutting materials into specific shapes and forms with a high degree of accuracy. As industries continue to evolve, precision die cutting has become increasingly vital in producing customized components across various sectors, from automotive to medical devices. This article delves into the intricacies of precision die cutting, exploring its applications, benefits, techniques, and future trends.
What is Precision Die Cutting?
At its core, precision die cutting involves the use of sharp metal blades—known as dies—that cut through materials (such as paper, plastic, rubber, or metal) to create specific shapes or designs. This process is often employed when high volumes of consistent, shaped material are required. The uniqueness of precision die cutting lies in its ability to deliver exact sizes and shapes repeatedly, making it ideal for manufacturing parts that require stringent tolerances.
Key Applications and Industries
Precision die cutting finds applications in a myriad of industries, each utilizing this technology to streamline production and enhance product quality. Here are several key sectors that benefit from precision die cutting:
- Automotive: Components such as gaskets, seals, and insulation materials are produced using precision die cutting to ensure proper fit and function in vehicles.
- Medical: The medical industry relies on custom die-cut parts for equipment, surgical kits, and packaging that meet stringent safety and precision standards.
- Electronics: Die cutting is used to manufacture insulating materials, conductive parts, and casings for electronic devices to ensure optimal performance and reliability.
- Packaging: Precision die cutting is crucial in the production of custom packaging solutions that protect products during transit while appealing to consumer preferences.
- Textiles: This process allows for the efficient cutting of various fabrics and materials, offering flexibility and precision in the fashion and upholstery sectors.
Benefits of Precision Die Cutting Technology
Adopting precision die cutting technology yields several advantages which can significantly enhance production efficiency and quality:
- High Precision: This method ensures that each part produced is virtually identical, maintaining tight tolerances that are essential for many applications.
- Cost-Effectiveness: While the initial investment in dies can be significant, the high volume production capabilities ultimately reduce costs per unit.
- Speed: Precision die cutting processes can produce thousands of parts in a fraction of the time compared to manual cutting methods.
- Versatility: Die cutting can handle a range of materials, allowing companies to customize products based on specific material properties and requirements.
- Reduced Waste: The precision of die cutting minimizes scrap material, leading to more sustainable manufacturing practices.
Types of Precision Die Cutting Techniques
Various die cutting techniques are employed depending on the specific requirements of the project. Understanding these methods is essential to selecting the most appropriate one for your application.
Rotary Die Cutting Explained
Rotary die cutting utilizes a cylindrical die to cut materials as they pass through the machine. This method is particularly effective for high-speed production runs and is noted for its ability to produce intricate shapes with speed and efficiency.
The rotary die cuts continuously, allowing for seamless production processes, especially in industries like packaging and labels. Operators can quickly change die sets for different shapes or sizes, which enhances flexibility.
Flatbed Die Cutting vs. Rotary
While both flatbed and rotary die cutting serve similar purposes, they employ different mechanics:
- Flatbed Die Cutting: In this method, a flat surface is used to hold the material in place while the die presses down to cut. This technique is often preferred for larger sheets and more complex designs, as it provides better control over material placement.
- Rotary Die Cutting: As mentioned, this method is more suited for continuous processes and high volumes. However, it may involve higher initial setup costs compared to flatbed systems.
Choosing between these methods depends on the specific requirements of each project, including material type, complexity, and production volume.
Laser Die Cutting for Advanced Applications
Laser die cutting is a modern and advanced technique that uses a focused laser beam to cut or engrave materials. This method offers unparalleled precision and versatility, making it an excellent choice for intricate designs and small batch production.
Some notable advantages of laser die cutting include:
- Flexibility: It can cut virtually any material, including difficult-to-handle substrates like thin metals and specialized films.
- Minimal Material Waste: The laser’s precision minimizes the amount of scrap material generated during production.
- Customization: It allows for quick adjustments to designs without the need for new dies, making it ideal for prototyping and small runs.
Selecting the Right Die Cutting Service
Choosing the right die cutting service provider is crucial for ensuring quality and efficiency in production. Several factors should be taken into consideration when making your selection:
Criteria for Choosing a Precision Die Cutting Provider
When evaluating potential die cutting services, consider the following criteria:
- Experience and Expertise: Look for providers with a proven track record in the industry and experience with your specific type of material and application.
- Quality Control Processes: Ensure the provider has robust quality control processes to maintain high standards throughout production.
- Technological Capabilities: Evaluate the range of cutting technologies they employ to ensure they can meet your specific needs effectively.
- Customer Service: Prompt communication and support can significantly enhance your experience, especially when dealing with complex projects.
Cost Considerations for Die Cutting Projects
Understanding the cost structure of die cutting services is fundamental to budgeting appropriately for projects. Factors influencing cost include:
- Die Costs: The price of creating custom dies can be substantial, depending on the complexity and material used.
- Material Costs: Different materials come with varying price points, impacting the overall project cost.
- Production Volume: Larger orders typically result in lower costs per unit due to economies of scale.
- Complexity of the Design: Intricate designs may require more complex dies, increasing both initial costs and production times.
Assessing Quality and Turnaround Times
Quality and turnaround time are critical factors in selecting a die cutting service. Ensure that the provider can meet your quality standards consistently while also delivering parts in a timely manner. Inquire about their production timelines, especially for high-volume orders, and check customer testimonials or references regarding their reliability.
Common Materials Used in Precision Die Cutting
A variety of materials can be effectively die-cut, and understanding material compatibility is essential for achieving the desired outcomes.
Understanding Material Compatibility
Not all materials are suitable for all die cutting methods. Compatibility with the chosen die cutting technique is crucial in ensuring that the final product meets the required specifications. Key factors to consider include:
- Material Thickness: Thicker materials may require more force and specialized dies, while thinner materials can often be cut more easily.
- Material Composition: Different materials respond differently to cutting methods; for instance, foams and fabrics may require distinct cutting techniques compared to metals or plastics.
- Surface Finish: The finish of the material may impact adhesion and the ability to hold shapes post-cutting.
Foams, Plastics, and Metals
Each category of materials presents unique characteristics:
- Foams: Commonly used in cushioning, insulation, and packaging. Precision die cutting creates clean and consistent shapes for effective use in various applications.
- Plastics: High-quality die cuts in plastics can result in strong, durable parts used in automotive, consumer goods, and packaging industries.
- Metals: Die cutting is employed in creating components for heavy machinery, electronics, and automotive parts, requiring specific considerations regarding thickness and tensile strength.
Choosing the Best Material for Your Needs
Choosing the right material for die cutting projects requires considering the final application, manufacturing process, and life cycle of the product. Engage with your die cutting provider for guidance on selecting materials that best suit both the intended use and budget constraints.
Future Trends in Precision Die Cutting
The precision die cutting industry is evolving in response to technological advancements and market needs. Staying abreast of future trends will help businesses remain competitive in a rapidly changing landscape.
Innovations in Die Cutting Technology
Recent innovations, including smarter automation and improved material processing techniques, are transforming precision die cutting. Technologies like digital die cutting are facilitating quicker design adjustments and improved customization capabilities, allowing manufacturers to adapt swiftly to market demands.
Sustainability Practices in Die Cutting
As sustainability becomes a growing concern for manufacturers, many die cutting services are adopting eco-friendly practices. This includes using recyclable materials, producing less waste, and implementing efficient production processes to minimize their carbon footprint. Engaging with providers who prioritize sustainability can not only enhance brand image but also appeal to environmentally-conscious consumers.
How Automation is Changing the Die Cutting Landscape
Automation is set to revolutionize the die cutting industry, enhancing speed and accuracy while reducing labor costs. Automated die cutting systems can operate continuously, minimizing downtime and maximizing productivity. Additionally, such systems can incorporate data analytics, optimizing operational efficiency through real-time monitoring and adjustments to the manufacturing process.