Your Go-To Source for Quality Welding Supplies and Essential Gear
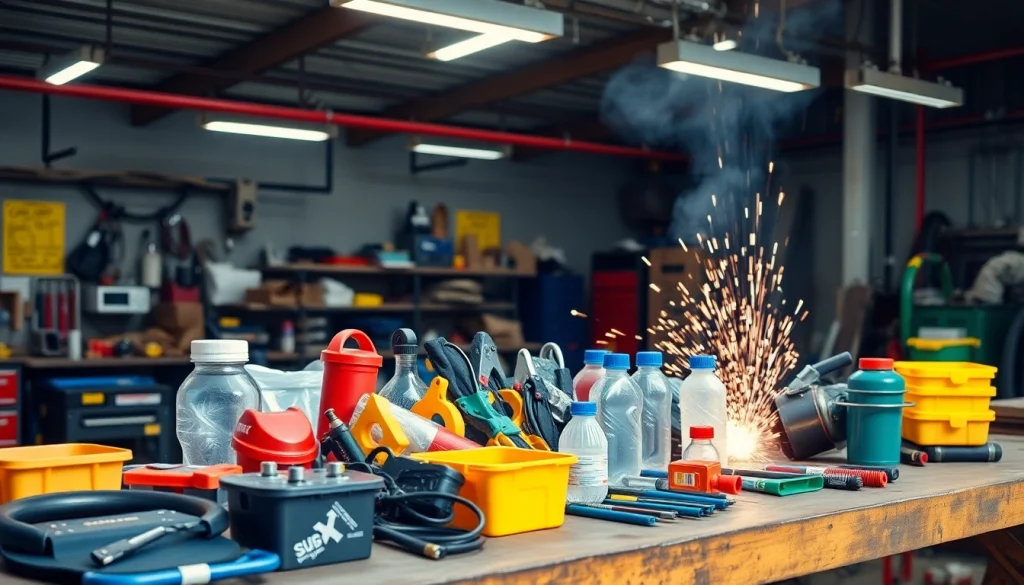
Understanding Welding Supplies: What You Need to Know
Welding is an essential process utilized across various industries to join materials together through fusion. For both amateurs and seasoned professionals, understanding the types of welding supplies necessary for different projects is crucial to ensuring safety and efficiency. From welding machines to protective gear and consumables, knowing what to use can significantly impact the quality of your work. This article will explore the different categories of welding supplies, how to choose the right equipment, and best practices for maintaining your gear.
Types of Welding Supplies
Welding supplies can broadly be categorized into the following segments:
- Welding Machines: These are critical for executing various welding techniques, including MIG (Metal Inert Gas), TIG (Tungsten Inert Gas), and Stick welding.
- Protective Gear: This ensures safety while welding. Important items include helmets, gloves, jackets, and boots.
- Consumables: Items like welding rods, wires, and gas cylinders fall under this category. They are used in the welding process but are consumed during operation.
- Tools and Accessories: Tools such as clamps, magnets, and pliers enhance the welding process by providing assistance in holding and positioning materials.
Choosing the Right Gear for Your Projects
Selecting the appropriate welding supplies for each project is vital. Factors to consider include:
- Material Types: Different materials require specific welding processes and techniques.
- Project Scale: Larger projects may need industrial-grade equipment, while smaller home projects may only require basic supplies.
- Experience Level: Beginners should opt for user-friendly devices, while professionals may seek advanced tools that allow for intricate work.
Understanding these factors will enable you to pick supplies that not only match your skill level but also optimize your project outcomes.
Common Welding Materials and Their Uses
Welding can be performed on a variety of materials, each requiring different welding supplies:
- Steel: The most common material used in welding due to its strength and versatility. MIG welding is frequently used here.
- Aluminum: Requires special equipment and techniques, typically TIG welding, due to its lower melting point.
- Stainless Steel: Needs careful selection of filler material and welding processes to avoid rust and staining.
- Cast Iron: Challenges include its brittleness and need for preheating; specialized rods may be necessary for effective welding.
Essential Welding Equipment for Every Welder
Every welder, regardless of experience level, should have a set of basic welding equipment on hand to ensure efficient and safe working conditions. Below are essential tools and equipment every welder should consider:
Protective Gear: Safety First
Safety gear is non-negotiable in welding. This includes:
- Welding Helmets: Protects the face and eyes from harmful ultraviolet light and bright arcs.
- Welding Jackets: Made from flame-resistant materials, these protect the skin from sparks and heat.
- Gloves: Essential for hand protection, they should be durable and offer a good grip.
- Ear Protection: Noise levels can become significantly high, making ear protection crucial during operation.
- Respirators: These are recommended for environments where fumes are present and must be managed.
Welding Machines: MIG, TIG, and Stick Options
The choice of welding machine often depends on the type of welding that will be performed:
- MIG Welders: Perfect for beginners and those looking to weld thicker materials quickly. They are user-friendly and versatile.
- TIG Welders: Provide high control and precision, suitable for thin materials and intricate welds.
- Stick Welders: A strong choice for outdoor jobs and thicker materials, as they can work in less than ideal weather conditions.
Choosing Accessories: From Helmets to Gloves
Welding accessories complement the main equipment and improve the quality of work. Important accessories include:
- Welding Magnets: Help hold pieces in place during work, ensuring accuracy.
- Clamps: Essential for securing workpieces together before and during the welding process.
- Welding Pliers: Used for handling hot materials and cleaning up after welding.
Where to Find Quality Welding Supplies Online
Finding reliable sources for welding supplies online can enhance the overall experience of your projects. Here, we will cover effective strategies for locating quality supplies.
Top Online Welding Supply Stores
Some of the leading stores for purchasing welding supplies online include:
- Cyberweld: Known for offering a wide range of welding supplies from brands like Miller and Lincoln Electric.
- Welding Supplies from IOC: They provide various welders and protective gear at competitive prices.
- WeldingOutfitter.com: Features a vast inventory, ranging from basic supplies to advanced equipment.
- Baker’s Gas & Welding: Offers high-quality welding gear and a strong customer service reputation.
Comparing Prices and Quality
When shopping for welding supplies, compare prices and read reviews to gauge quality. Key aspects to look for include:
- Brand Reputation: Brands with a solid history in the industry tend to offer higher quality products.
- Warranty and Return Policies: Look for suppliers that offer warranties on their equipment and have favorable return policies.
- Shipping Policies: Consider stores that offer free or affordable shipping rates without compromising service quality.
Customer Reviews: What to Look For
Reading customer reviews can provide insights into product performance and customer satisfaction. Pay attention to:
- Product Durability: Look for reviews mentioning the longevity and resilience of the welding supplies.
- Ease of Use: Especially for machines, feedback on user-friendliness is essential for all skill levels.
- Customer Service: Responses from sellers, particularly in cases of dissatisfaction or product issues, are critical for long-term relationships.
Best Practices for Maintaining Your Welding Equipment
Effective maintenance is crucial for extending the life of your welding supplies and ensuring optimum performance. Implementing regular maintenance practices can save time and money in the long run.
Cleaning and Storing Welding Supplies
Proper storage and cleaning can significantly impact the longevity of your tools and machines:
- Clean Regularly: Remove slag, spatter, and other residues after each use to avoid corrosion and damage.
- Store in a Controlled Environment: Keep tools in a clean, dry place to prevent rust and degradation.
- Use Cases and Covers: Protect machines and accessories with appropriate cases to safeguard against dust, moisture, and scratches.
Regular Maintenance Tips
In addition to cleaning, carry out regular checks on your equipment:
- Inspect Cables and Hoses: Look for signs of wear and tear to avoid safety hazards.
- Check Connections: Ensure all connections are tight and free from corrosion to maintain optimal performance.
- Lubricate Moving Parts: Regular lubrication can reduce wear and tear on mechanical components significantly.
Identifying When to Replace Equipment
Understanding when to replace welding supplies can save money and improve safety:
- Signs of Damage: Quantity of cracks, breaks, or excessive wear on equipment should prompt replacement.
- Performance Issues: If your supplies frequently malfunction or underperform, it may be time to invest in new equipment.
- Safety Standards: Ensure that gear meets the latest safety standards; outdated equipment may put you at risk.
Troubleshooting Common Welding Problems
Even experienced welders encounter problems. Understanding how to troubleshoot common issues can save time and enhance project quality.
Identifying Issues with Welding Supplies
Many common problems can arise during welding, often tied to equipment issues. Here are some signs to watch for:
- Poor Arc Start: An inconsistent or difficult arc start may indicate an issue with the welder’s settings or the electrode.
- Excessive Spatter: Can be caused by improper voltage or wire feeding rates, requiring adjustment or re-calibration.
- Weak Welds: Insufficient welding speed or incorrect materials can result in weak welds that compromised structural integrity.
Basic Repairs for Your Welding Gear
Performing basic repairs on your equipment can extend its life and maintain performance:
- Replace Consumables: Ensure that you replace worn-out welding wires, rods, and protective gear regularly to maintain quality.
- Fix Cable Insulation: Address frayed cables by repairing or replacing them to prevent short circuits and ensure safety.
- Calibration: Regularly calibrate machines according to the manufacturer’s guidelines to prevent issues related to pressure and flow.
When to Seek Professional Help
Some problems are beyond basic repairs and may require professional assistance:
- Complex Electrical Issues: If faced with recurrent electrical problems, seek a professional technician to avoid risk of electrical shock.
- Structural Damage: If your equipment has significant physical damage, professional assessment is necessary to determine safety and usability.
- Value of Upgrades: Evaluating the cost-effectiveness of repairs versus purchasing new equipment should ideally involve expert advice.